Before we had any PAT tools, the process was like a black box to us. We put something in and get something out without knowing what happened inside. Now, we have an ‘Eye’ to look inside that black box and see what’s going on in there.
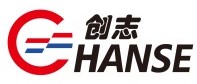
Capture the real-time data analysis of your bulk powder processes automatically with our powder and bulk solid particle size analyzer. Troubleshoot and improve end-product goals with particle size and shape data. Adopt automated process control to drive down production cost. Non-product contact automation minimises risk with hazardous materials.
Manufacturers are leveraging more data into operations by embedding intelligent devices to increase functionality. Eyecon2 is Pharma 4.0 ready and compatible with the connected devices mantra of the Internet of Things. Using direct image analysis, our particle size analyzer can deliver more efficiency and accuracy than laser diffraction technology to measure particles.
Eyecon2 particle analyser can be implemented anywhere powders flow. In-line, non-product contact measurement for both Batch and Continuous processes, removing the need for sampling. Optimise product transfer and scale-up, Eyecon2 can follow and define the journey from lab to pilot to production scale, saving time and cost.
Eyecon2 underpins QbD by affording the ability to control and predict critical quality attributes (CQAs). Knowledge of particle size and shape reveals the functional relationships linking material attributes and critical process parameters (CPPs). Eyecon2 is an enabler of Continuous Process Verification.
Eyecon2 , our non-product contact, real time particle size and shape data analyser has had a significant software upgrade. EyePASS the particle size image analysis software now utilizes cutting edge Artificial Intelligence (AI) and machine learning.
Capture the real-time data analysis and profile of your dry powders and bulk solids with Eyecon2 particle size analyser. Troubleshoot and improve end-product goals with particle size and shape data. Adopt automated process control to drive down production cost. Non-product contact measurement minimizes risk with hazardous materials. At-line and in-line configurations allow transition from benchtop to in-line integration and evolve with your needs. EyePASS the Image analysis software now utilizes cutting edge Artificial Intelligence (AI) and Machine Learning (ML)
The AI upgrade transforms the versatility of the Eyecon2, vastly expanding the range of material types that can be measured in real time and drastically improves particle size and shape detection for materials that were previously unviable for image analysis. One of the primary steps performed by our image analysis software EyePASS is particle segmentation i.e., the detection and delineation of particles from the images sent by the Eyecon2. All measurements reported by the software are based on the results of the particle segmentation step.
Convolutional neural networks (CNN) iterate the trained images, assigns weights and biases to assorted objects in the image, differentiate one from the other and improves the feature of interest extraction from new unseen image data. This means EyePASS V 3.0 with ML image analysis unlocks the full power of particle size and shape analysis. ML image analysis negates difficulties with the traditional computer vision constraints of illumination and classification of materials with light absorption or light reflective properties. i.e dark materials, reflective materials etc. can now be measured for particle size distribution.
Size Range | 50 – 5500 μm |
Principle Measurement Method (non-product contact) | Direct Imaging |
Size Measurement Data | D10, D25, D50, D75, D90 in numeric and volumetric with Mean and Median values all trended in real time with live histogram and S-curve results. Includes process deviation alarm. |
Exportable Data | PDF report of recording session, CSV file with data on every image analysed with full PSD from D5-D95, captured images exportable as JPEG |
Data Processing | EyePASSTM real time particle analysis software installed on a dedicated IPC/PC/Laptop with Windows 10 |
Measurement Time | ~ 5 seconds per image |
Material Speed (max.) | ≈ 10 m/sec |
Shape Measurement Data | Eccentricity Average, Eccentricity RSD, Range 0-1 |
Dimensions & Weight | Eyecon2 | 250 x 128 x 132 mm (4 kg) |
Connection Hub | 254 x 170 x 57 mm (1.2 kg) | |
Eyecon2 inc. Automated Benchtop Stage | 300 x 190 x 480 mm (7.8 kg) | |
Power | 230VAC @ 50HZ / 110VAC @ 60HZ | |
Casing Materials | 304 Stainless steel, Glass window, Silicon gaskets | |
Connection Cable | From Eyecon2 to Connections Hub via Speedcon quick-release power & data cable, available in lengths up to 25 m. From Connections Hub to IPC/Laptop via USB |
Illumination Source | 12×3 High intensity, low energy R,G,B LEDs |
Image Area | 11.25 mm x 11.25 mm |
Pixel Size | 5.5 μm x 5.5 μm |
Resolution | 2046 px x 2046 px |
Exposure Duration | 5 μs |
Sensor | CMOS |
GMP | EyePASS is both 21 CFR part 11 & GAMP5 Compliant |
Communications | EyePASS is Open Platform Communications compatible with OPC UA & OPC DA 3 |
With InnoGlobal Technology’s team of mechanical, electronic, and application engineers, we have extensive experience collaborating with process experts to achieve successful measurement and process integration solutions from the equipment level with Eyecon2, to integration with automated software platforms, such as SmartX, for advanced process control.
For peace of mind, we invite customers to undertake a trial of their material at our Ireland application lab (with optional customer attendance). Where we offer sample analysis with Eyecon2 particle size analyzer. Trials can also replicate real-world conditions with a wide range of processing equipment available to offer assurance that Eyecon2 can meet their analytical requirements.
We at InnoGlobal Technology work with industry scientists and engineers to understand the challenges they face, and the risks when embedding new technology. Whether it’s a standard benchtop system or a custom In-line design, InnoGlobal Technology aims to help facilities get to market faster, improve process understanding and achieve higher standards of quality by offering versatile solutions suited to their needs.
We help customers unlock the full potential of Eyecon2 by offering a number of accessories and services. On-site training ensures users are confident with the technology, while top-notch customer support and extended maintenance contracts ensure you’re never more than a phone call away from help when needed. A Verification Standards Kit (VSK) offers an easy, traceable and certified method for system calibration/verification, and our IQ OQ template streamlines the qualification process, with optional on-site execution by our own expert engineers.
InnoGlobal Technology’s window wiper system offers a GMP and ATEX compatible solution for maintaining the clarity of viewing ports when using exceptionally ‘sticky’ material during fluid bed processing. This helps to ensure robust and accurate measurement with InnoGlobal Technology’s Eyecon 2 or other optical / spectroscopic sensors relying on measurement through a viewing port.
Eyecon2 , our non-product contact, real time particle size and shape data analyser has had a significant software upgrade. EyePASS the particle size image analysis software now utilizes cutting edge Artificial Intelligence (AI) and machine learning.
Capture the real-time data analysis and profile of your dry powders and bulk solids with Eyecon2 particle size analyser. Troubleshoot and improve end-product goals with particle size and shape data. Adopt automated process control to drive down production cost. Non-product contact measurement minimizes risk with hazardous materials. At-line and in-line configurations allow transition from benchtop to in-line integration and evolve with your needs. EyePASS the Image analysis software now utilizes cutting edge Artificial Intelligence (AI) and Machine Learning (ML)
The AI upgrade transforms the versatility of the Eyecon2, vastly expanding the range of material types that can be measured in real time and drastically improves particle size and shape detection for materials that were previously unviable for image analysis. One of the primary steps performed by our image analysis software EyePASS is particle segmentation i.e., the detection and delineation of particles from the images sent by the Eyecon2. All measurements reported by the software are based on the results of the particle segmentation step.
Convolutional neural networks (CNN) iterate the trained images, assigns weights and biases to assorted objects in the image, differentiate one from the other and improves the feature of interest extraction from new unseen image data. This means EyePASS V 3.0 with ML image analysis unlocks the full power of particle size and shape analysis. ML image analysis negates difficulties with the traditional computer vision constraints of illumination and classification of materials with light absorption or light reflective properties. i.e dark materials, reflective materials etc. can now be measured for particle size distribution.
Over the years our customers have asked very insightful questions about the field of particle size and image analysis, the following list of questions are a selection of the most frequently asked. If there is a question that is not answered here, please contact us.
Analytical methods like image analysis can be powerful tools in revealing more about particles, for example their size and shape and in turn their behavior in terms of end product quality. In fact, measuring shape is one of the major benefits Image analysis has over other light scatter-based technologies. Eyecon2 is a smart particle image analyzer that combines the advantages of microscopy and digital particle analysis and enhances them. Eyecon2 measures particles from images in real-time by taking hundreds or thousands of measurements per image and reporting particle size and shape automatically, this digital information can then be communicated over protocols like OPC to not just report the particle size and shape but to control it. Eyecon2 is used in production environments to monitor and log product quality digitally and in R&D environments to investigate the changing process parameters like RPM, airflow, temperature, etc. have on particle size and shape in real-time.
Non-product contact means Eyecon2 is not in direct contact with the product it is measuring. It is a camera-based system that when mounted in-line is typically looking through a process window at a distance ranging from 0-25mm away from the product. Because of its non-product contact nature, it requires less change control to install into a controlled environment as it poses less of a risk to the product. The non-product contact allows Eyecon2 to measure products in hazardous ATEX zones. Plus, non-product contact does not interfere with the process itself, potentially modifying the particles it is measuring.
The Eyecon2 can measure bulk solids between 50µm – 5500µm
Any Industry where bulk solids particle size and shape advances end product quality, quantity, and the bottom line. Hence Eyecon2 has seen mass adoption in pharmaceutical manufacturing. Other Industries Eyecon2 is sold into include:
Chemical, Mining, Food & Feed, Construction, Energy. Because it is a smart particle image analyzer it can instantly digitally transform industries that log sieve analysis via pen paper methods to benefit from automated particle size analysis.
No, Eyecon2 is not suitable for measuring materials that are suspended in liquid due to a few reasons, particles in a medium when looked at with a camera change in size due to the light path and magnification effect of the medium. Eyecon2 is designed to measure wet solids such as materials wetted in a fluid bed coater or twin-screw granulator.
Incorporating Machine Learning into particle image analysis has revolutionized the capability of Eyecon2 . You can now measure entirely new material types such as glass beads, crystals, Urea, Oxides, among others. This expands not only capability but flexibility for future developments in image analysis.
An overview of how machine learning works in conjunction with Eyecon2 can be reviewed here.
At-line analysis involves the analytical device being located near the process where a sample from the process line is rapidly analyzed.
Off-line analysis involves the analytical device being located away from the process line where it was produced. It means sending a sample to either an on-site or off-site laboratory for analysis.
On-line analysis involves the analytical device being located on the process line, where the product is being passed by the analytical device, typically via a type of bypass valve. In-line analysis involves the analytical device being located in the process line itself, for direct measurement right where the product is being made so there is little to no risk of sampling error.
A simple way to differentiate At-line, Off-Line, On-line, and In-line is to add the word “the” in the middle. So, At-line means the measurement happens ‘at the line’. Off-line means the measurement happens ‘off the line’ and so forth. On-line and In-line are often confused a simple way to distinguish between the two is to ask, ‘is the product being brought to the analytical device? (On-line), Or is the analytical device being brought to the product? (In-line)’.
Eyecon2 is a non-product contact device. It is a camera-based technology and will either view through a window or onto a chute to measure particles. Integration in-line can be via a simple bracket, or it may require a more complex integration solution for example it may require an anti-fouling mechanism or have a new window fitted into a process. As important a question to ‘how can it be integrated?’ is to ask ‘where’ it should be integrated? because analyzing representative product is key to reliable results. Innopharma Technology has over 10 years of experience installing devices in-line. We offer ‘off the self’ solutions as well as the expertise to design, fabricate and integrate a solution suitable to your process needs. Please see below a selection of various in-line integration solutions.
The best way to get in contact is through the ‘Start a Conversation’ enquiry at the bottom of this page so we can arrange a call together and find out more about your needs for particle analysis.
Eyecon2 can measure non-uniform materials such are granular shaped materials. Regardless of the particle profile, the 2D area of the particle is converted into an equivalent elliptical area and converted into a 3D spheroid to calculate volume.
The new machine learning version of EyePASS V3.0 can accurately measure transparent or reflective materials thanks to trained machine learning models deployed to run in real-time in the software.
Eyecon2 operates very much like a digital microscope. For at-line analysis, this distance is fixed by mounting Eyecon2 onto the benchtop Autostage. For In-line integration, It has to be precisely located between 0-25mm away from the material depending on factors such as the process window’s glass thickness. This distance can be calculated, and an integration solution offered after a conversation with Innopharma Technology.
Yes, the coating thickness or film thickness can be derived by subtracting the starting particle diameter from the current particle diameter and dividing by 2. As the material is being coated the Eyecon2 will detect a change in a particle size and show it in real-time. Please refer to our application note titled Real-Time Prediction of Polymer-Coated Multiparticulate Dissolution using Process Analytical Technology for more information.
In particle image analysis, the images undergo a pixel segmentation step to determine the location of the boundary or the edge between the particles’ foreground, the substrate background, and from particle to particle. This segmentation is aided by the unique crossover of
Red, Green & Blue light illumination method from Eyecon2 where the boundary from one particle to the next can be easily identified when compared to other methods of black-and-white image processing.
In particle image analysis, after segmentation processing, a major and minor axis are fitted per particle. The major axis is the longest cord length that can be drawn through the particle and the minor axis is the shortest cord length that can be drawn through the particle that continues to be perpendicular to the major axis. The corresponding ellipse is converted into a 3D spheroid to calculate volume from which when all the particles are calculated together so the D number can be reported as a distribution or Particle Size Distribution (PSD).
Eyecon2 can measure the particle size and shape of bulk solids between 50 and 5500μm. But when measuring a particle within its size range it can detect a change as small as 5µm. For a Coating/Wurster process, Eyecon2 can detect growth in film thickness as low as 5µm.
Yes, although Eyecon2 does not directly report the percentage of drug loading, the real-time particle size data is used together with the loss on weight data of the spray binder from the balance or scales to calculate the percentage of drug loading. This can be elaborated on in this study
There are several things to consider when integrating Eyecon2 in-line onto a pre-existing process window. Such as, are the particles that are presented to the window going to represent the entire particle size distribution within the process? What is the aperture/size of the window opening? What is the thickness of the glass? As a guide mounting Eyecon2 requires a window with a minimum opening of 50mm and a maximum thickness of 20mm. For a free In-line assessment of your process window please contact us.
In-line particle image analysis relies on the camera of Eyecon2 being able to capture images of free-flowing particles. If the material the camera is looking at is not moving, as in the process window is blocked up with material or ‘fouled’, then no new particles are being presented to the camera for image capture. This is an issue. Thankfully Innopharma Technology have several anti-fouling solutions available. These can range from the non-invasive such as a change of window material to reduce fouling or to the more invasive solutions such as a gas purge mechanism or wiper mechanism. Get in contact through the ‘Start a Conversation’ enquiry at the bottom of this page so we can arrange a call to find out more about your needs.
The International Organization for Standardization (ISO) has several standards that apply to methods of particle measurement. The ISO 13322 series are the applicable standards for particle image analysis.
ISO 13322-1:2014 Particle size analysis — Image analysis methods — Part 1: Static image analysis methods
ISO 13322-2:2021 Particle size analysis — Image analysis methods — Part 2: Dynamic image analysis methods
These two standards go into detail about the considerations around particle measurement via image analysis with the differentiator between them being one is about static image analysis, the particles are at rest when images are captured and the other dynamic image analysis, where the particles are in motion when an image is captured.
Other relevant standards for particle measurement.
ISO 13320:2020 Particle size analysis — Laser diffraction methods
ISO 17867:2020 Particle size analysis — Small angle X-ray scattering (SAXS)
ISO 19430:2016 Particle size analysis — Particle tracking analysis (PTA) method
ISO 22412:2017 Particle size analysis — Dynamic light scattering (DLS)