Unravelling ATEX – A Guide for Everyone
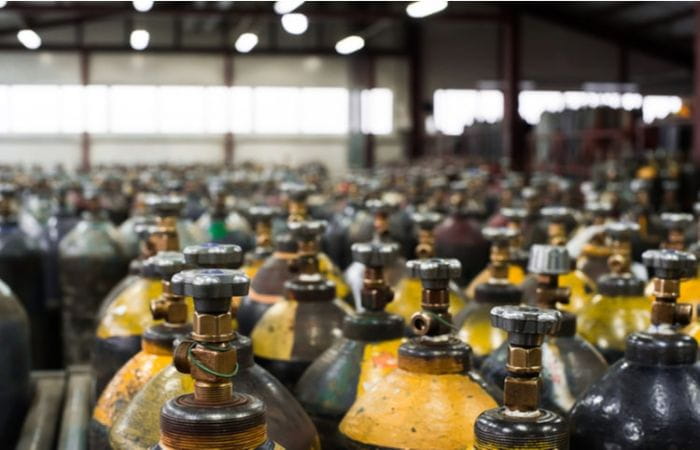
Because several standardisation bodies have input into the ATEX regulatory standard, the descriptive markings used by these multiple bodies can be a point of confusion, as often the markings are similar. For example, markings like II and IIG can prove perplexing. “II” indicates non-mining applications, whereas “IIG” is a gas safety marking from CENELEC.
Our first blog of a two-part series will demystify the basic principles and markings of ATEX while using the example of our particle size analyser Eyecon2 to demonstrate ATEX compliance.
ATEX background and history
The industrial revolution made it possible for the advancement in technology and manufacturing we see today, but I doubt many of us would switch places with those working in the dangerous conditions our ancestors were subjected to. Thankfully, regulations developed to ensure that the workplace and the equipment in it are designed with our safety in mind. One such necessary regulation is ATEX. This regulation is designed for the safety considerations of potentially hazardous explosive environments throughout the European Union (EU) but is also accepted by many organisations working in countries outside the EU.
The ATEX Directive describes a hazardous area as any location where there is a risk of an explosion due to the presence of flammable gas and vapours.
ATEX (equipment intended for use in ATmosphere EXplosible) is the combination of two EU directives to meet the minimum safety requirements for an explosive risk.
- Workplace – ATEX 137 Directive 1999/92/EC
- Equipment – ATEX 214 Directive 2014/34/EU
These directives began as French legislation that was adopted for use by the EU and which also forms the basis of IECEx -the international system for certification of equipment for use in explosive atmospheres.
Why ATEX?
A series of unfortunate events prompted the formation and the subsequent enforcement of the ATEX regulation.
One of the earliest recorded dust explosions was in 1785 at Giacomelli’s Bakery, Italy. A baker’s boy was shovelling flour under an open flame, an action which caused the resulting flour cloud to ignite with a ferocity to blow the windows and their frames out into the street. The boy suffered scorches to his arms and face.
In 1983, The Aluminium Powder Co-operate, a plant situated in Anglesey, North Wales, was atomising molten aluminium into a stream of compressed air. The mixture resulted in an explosion that injured two people. This incident received notoriety due to the pictures showing the extensive plant-wide damage.
Sadly, time and again, we have been shown the importance of why potentially explosive environments have to be treated with due care. ATEX imposes requirements for companies to protect their employees from the risk of explosion. It is important to remember that every environment is different, and each has specific requirements depending on the nature of the atmosphere and the elements that are present within it.
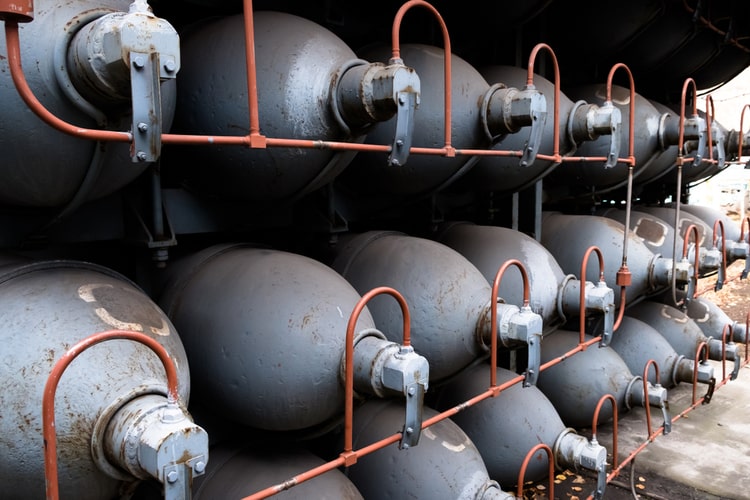
Explosive Environments Ex
Potentially explosive environments, or ‘Ex’ areas, have different levels of risk and are categorised into zones in the workplace where equipment is operated. The classification is based on the explosive risk being either gas, or dust, or both. ATEX certified equipment will state the environments they can safely operate within.
ATEX zones and protection classifications
There are zones categorised separately for dust and gas, where gas zones are identified as being one numeric character long, i.e. 0,1,2 and dust zones are identified by the addition of a ‘2’ character, i.e. 20,21, 22. In both cases, the last digits 0,1,2 identify the type of zone.
For instance, 2, 21 indicates that a combustible gas is not likely to be present in normal operation, but a combustible dust is likely to be present in normal operation.
So, what exactly is not likely when considering the presence of gas or dust in normal operation? These are not terms engineers and scientists are comfortable with, but thankfully, the ATEX directive has quantified ‘not likely’ to be less than 10 hours a year.
In part 2 of our ATEX blog series explores equipment classification and breaks down the exact meaning of the ATEX labels.
If you require more information on ATEX to further demystify the subject, get in touch!