To Industry 4.0 and Beyond
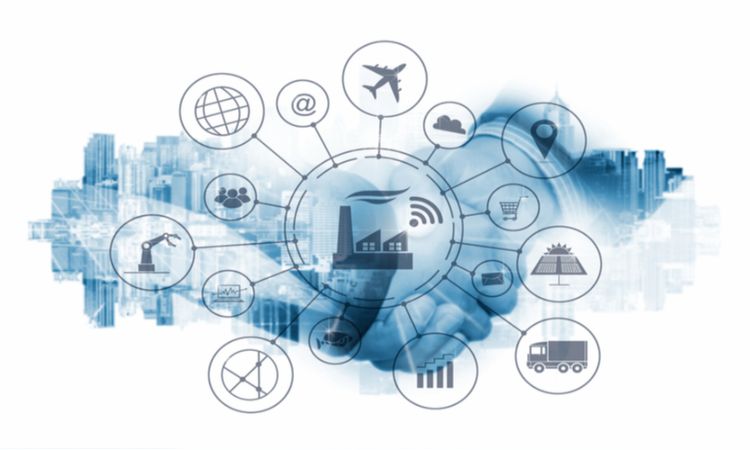
It takes putting things into perspective to appreciate how far the digital transformation has come. In such a short space of time from when the first PCs became affordable, we’ve seen the rise of the smartphone, and now, the proliferation of IoT (Internet of Things). The data produced by the sheer amount of devices has allowed fledgling artificial intelligence (AI) to become mainstream and accepted as a means of data analysis. Everything from targeted advertising to weather apps now uses AI as its backbone. Generally, our potential for information gathering and analysis has been limited. That is, until the digital revolution. Lean Six Sigma has been an industry game-changer, shifting our industrial mindsets from a static to a dynamic constant improvement model. However, the dawn of the fourth industrial revolution or industry 4.0 is upon us.
What is Industry 4.0?
Industry 4.0 builds on the principles of the automation revolution, adding increased interconnectivity and insight to manufacturing through the use of digital technologies such as Artificial Intelligence, Big Data and the Internet of Things (IoT), which are applied through the use of Smart Machines. Ever since James Watt implemented the Watts Governor to regulate the infant steam engine and quantify its output, engineers and scientists have sought better understanding and control of industrial processes.
The interconnectivity of Industry 4.0 allows ad hoc organisational integration. This is done with far more flexibility and less overheads than ERP systems. It can be integrated into existing systems, can be completely separate, or a mix of both.
What Are The 9 Pillars Of Industry 4.0?
Industry 4.0 comprises of 9 pillars. Each pillar represents a digital technology that manufacturers are adopting in order to enhance their production process. The application of these technologies combined allows companies to embrace smart production and optimise their processes, boosting productivity and efficiency.
The nine pillars of industry 4.0 are;
- Data Analytics
- Industrial Internet of Things (IoT)
- Autonomous Systems
- Cloud
- Cyber Security
- Simulation
- Horizontal and vertical integration
- Augmented Reality
- Advanced Manufacturing
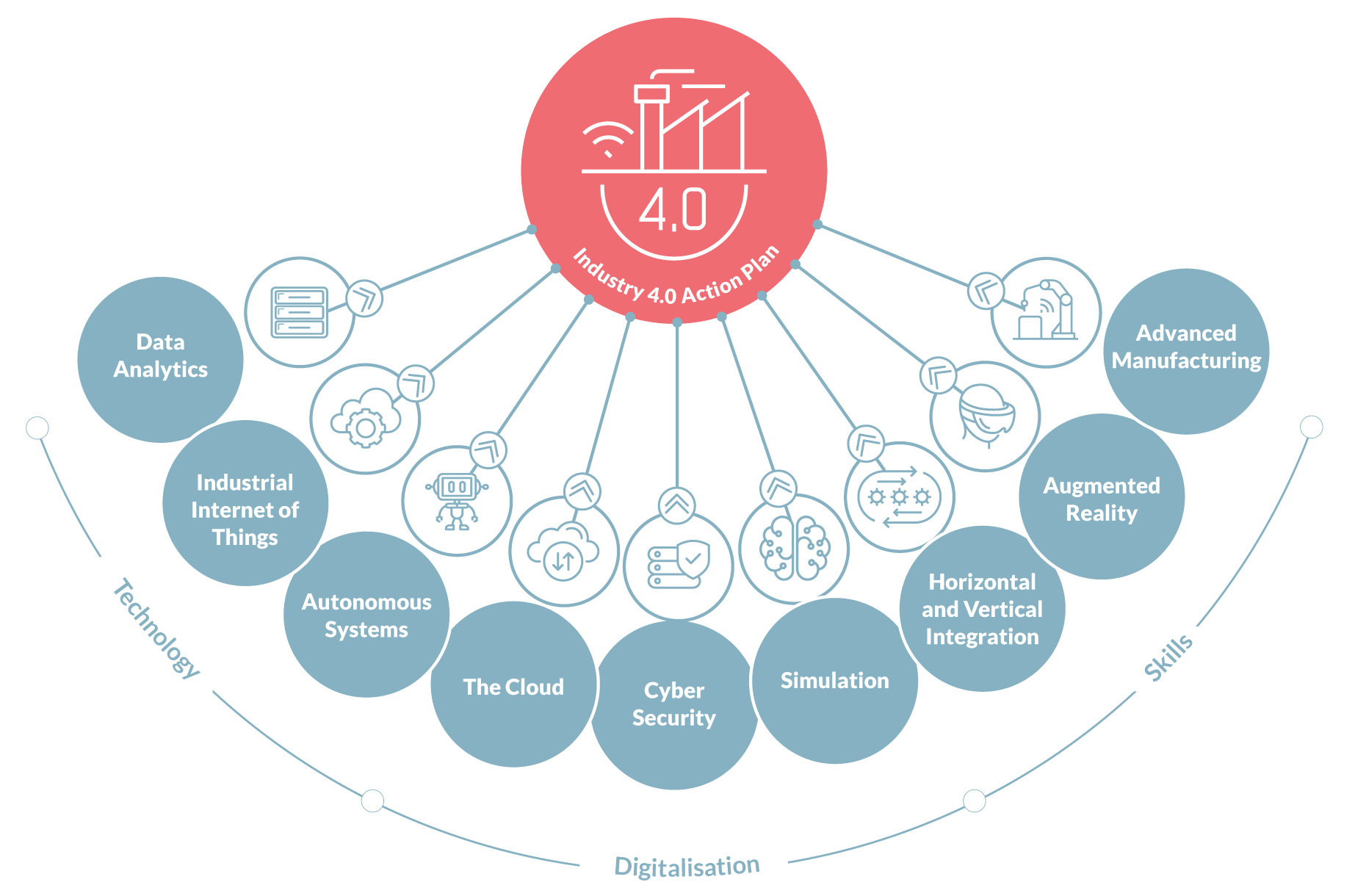
The Outbreak Of Covid-19 And The Rise In Industry 4.0
During the COVID-19 outbreak, the need for decentralized manufacturing and smart factories became apparent. The need to access relevant information remotely is critical and is likely to become a permanent requirement for the industry. The advantage of Industry 4.0 for this is not only the ability to interact with data and processes remotely but also in the breath of the data that can be collected. Insights can be made from data that at first may be less obvious but can prove important in analysing a process, pre-empting an equipment malfunction or determining a quality attribute.
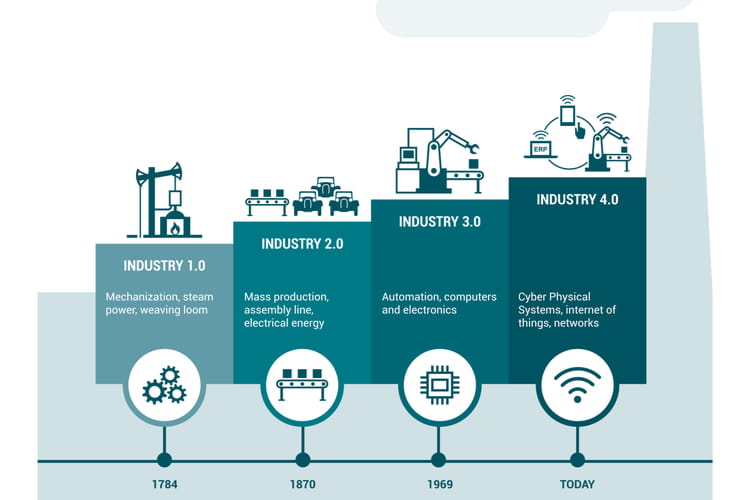
Benefits Of Industry 4.0 For Pharma
In Pharma, Industry 4.0 is being used as a process control tool. But more than this, the data generated can be leveraged to deepen process understanding. This is revealing insights into processes that were previously inaccessible.
Industry 4.0 allows us to leverage diverse quantitative and qualitative data, like those from industrial processes, human-generated, and sensor-driven data to fully understand the process and workflow. Everything from conventional statistical tools to AI-driven solutions can be used to generate a complete process model for diagnostics, real-time process control, process development, and process scaling.
In oral solid dose processes like fluid bed granulation, twin-screw extrusion, and tablet compression, Industry 4.0 can use diverse sensor data, and even operator experience, to build a picture of the process. With a bigger, more complete picture, we can characterise processes better. The utility of all this data is immense. We can use it to control the existing process, design new processes, and scale processes from lab to production.
Remote access to data, both retrospectively and live processes, lets us easily transfer knowledge between sites. The benefits of ensuring consistency by removing human variability are huge. The age of lost processes information is over. Automatic documentation generation captures any and all process adjustments.
How Innopharma Can Help You Embrace Industry 4.0
While it may sound daunting to consider integrating diverse technologies onto either an existing or new process, the workflow can be made considerably more manageable by using a vendor with direct experience in the industry, knowledge of regulatory and internal requirements, such as FDA 21 CFR Part 11, conscious of GMP principles, as well as having a deep understanding of the physical processes. InnoGlobal Technology (formerly Innopharma Technology) has the services available to help you take advantage of the opportunities that adopting industry 4.0 offers. InnoGlobal Technology’s (formerly Innopharma Technology) consultancy services can help you merge industry 4.0 into your business model by advising on integration into your systems and where best to host your data, be it locally, on the cloud, or a combination of the two.
This has the advantage of reducing the learning curve. By eliminating trial and error, you ensure the most appropriate equipment is integrated into your facility and the right data and functionality are accessible where you need it. Our consultancy can assess whether a complete factory-wide Industry 4.0 integration is optimal. We can equally advise a much smaller single process tool integrations and ensure that the scale is appropriate to your needs.
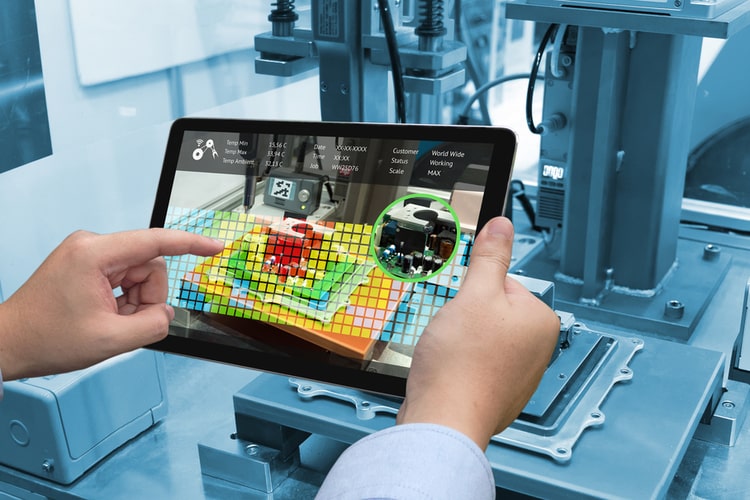
SmartX: An Industry 4.0 Technology
SmartX process automation from InnoGlobal Technology (formerly Innopharma Technology) is our Industry 4.0 system designed specifically around the pharmaceutical industry aimed at OSD processes. It allows agnostic integration of sensor and process equipment into the system. That lets you connect with a vast array of sensor and process equipment -not just those belonging to one or a couple of specific companies. The development of process controls is created in an intuitive environment with a large selection of process templates available. These can be used for reference or to build custom processes. This approach allows data to be stored in a way that’s convenient for you. Whether locally, on the cloud, or a combination of both, the data can also be easily integrated into your existing systems.
Our SmartX system has been successfully integrated into Fluid bed Granulation, Coating, and Twin-screw granulation leading to substantial gains in process understanding, process improvement, control, and access to data.
At InnoGlobal Technology (formerly Innopharma Technology), regulatory compliance, and the integrity of your data is our first priority. We ensure full FDA 21 CFR Part 11 compliance and GxP compatibility for all our systems. Our consultancy services mean you have a partner with experience when navigating the road to Industry 4.0 and allows you to achieve its maximum value.
If you would like to know more about how InnoGlobal Technology (formerly Innopharma Technology) can help you embrace industry 4.0, get in touch with our team today.
For more exciting developments in this space, follow us on LinkedIn and Twitter.