Pharma 4.0: Integrating Multieye₂ Near Infrared Spectrophotometer with SmartX
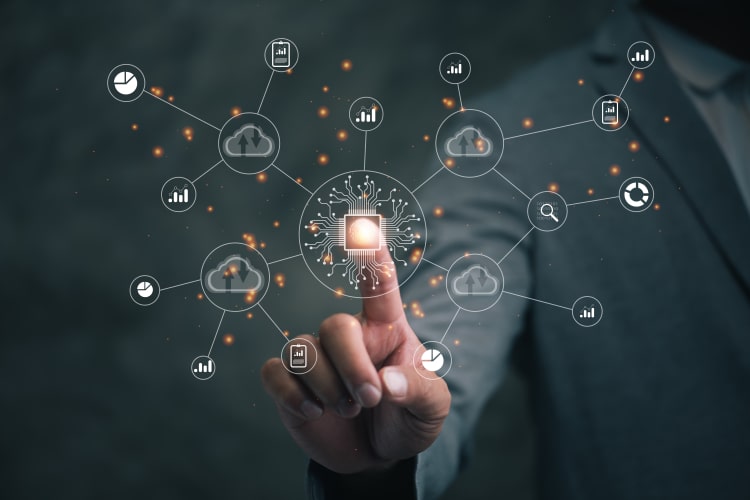
Recent advances in sensor technology and machine learning have opened a new horizon in the use of Process Analytical Technology (PAT) in Oral-Solid Dose manufacturing. The next industrial revolution involves the automation of production processes, and it’s coming to the pharmaceutical sector – Pharma 4.0.
Regulators across the world, including ISPE and the FDA, are encouraging Pharma manufacturers to adopt methods for real-time process monitoring and automation. The move to automation promises improved manufacturing efficiency, reduced burden on time-consuming and costly laboratory analysis, fewer reworks, and less waste.
So how is this achieved? To automate a process, you need to know what your process is doing and how to adjust the process inputs accordingly. At InnoGlobal Technology (formerly Innopharma Technology), we have developed a suite of integrated tools to do all of this for you.
You can monitor critical quality attributes in real-time using state-of-the-art PAT sensors such as the Multieye2 Near Infrared Spectrophotometer. This sensor has been developed specifically with real-time in-line applications in mind. With extremely fast acquisition times, very high signal to noise, automated referencing, and multiple probe options, it is ideally suited to monitoring production from granulation, roller compaction, drying, through to compaction, and tableting.
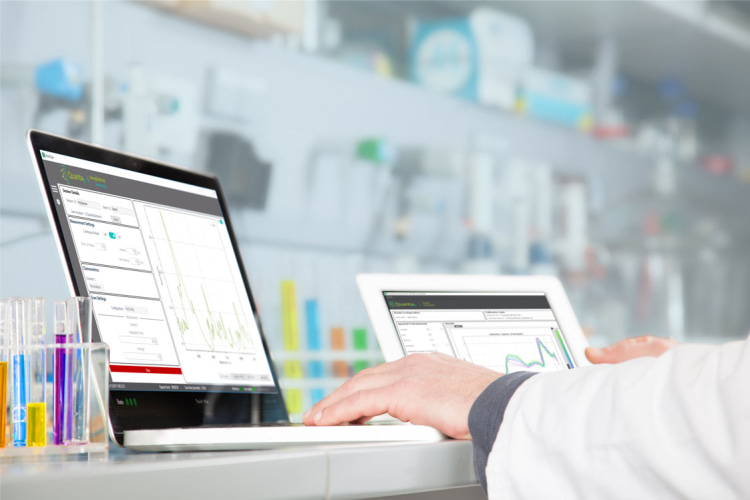
Our sensors integrate natively with a wide range of data historians and process control systems via OPC standard protocols, including our in-house developed advanced data platform for process development and automation, SmartX, which reads in process-equipment and sensor data, determines whether the quality attributes are within specification, and adjusts the critical process parameters accordingly, without requiring intervention from technical staff.
To achieve this, several reference runs are carried out to determine typical operating trends and to establish the influence of process parameters, as is typical during process development. We can use the same process runs to train both SmartX and the Multieye2 NIR sensor, building calibration models and validating how well the models predict the critical quality attributes at the same time as mapping out how the product evolves throughout the process and in response to combinations of the parameters. The result is a data-driven tool that significantly accelerates development, gives real-time process data, and allows you to see how closely your process is tracking ideal process evolution. Check out our app note on our self-guided fluid bed granulation process here.
If you are interested in finding out more, please contact our team of PAT integration experts.