Decentralizing Manufacturing Because of COVID-19
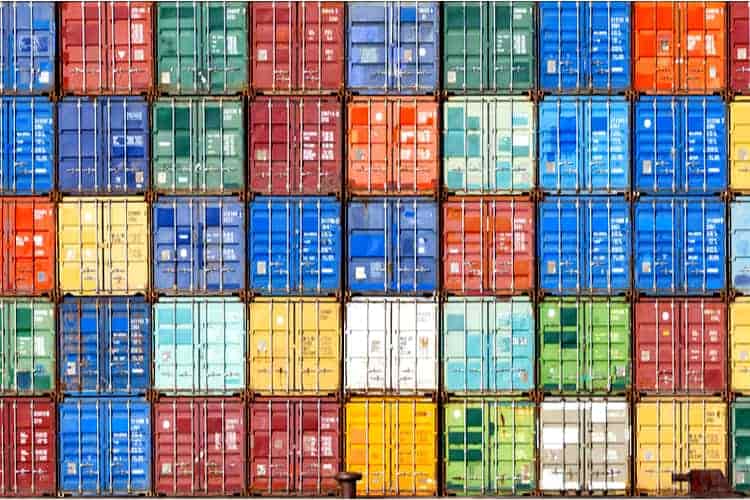
This year has been turned on its head because of COVID-19. With a rapid shift to remote working overnight, we have found ourselves in uncharted waters. As we adapted to life working from home, what impact has this had on the current manufacturing industry? We explore what has already changed and what will change in the future.
Until now, manufacturing has been highly globalized, with many manufacturing sites working together across the globe to make a finished product or device. Taiichi Ohno of Toyota was a pioneer of just-in-time (JIT) manufacturing. This management philosophy leads to extremely efficient production and is now a cornerstone for many in modern manufacturing. The risk with this methodology is its reliance on a very structured and steady supply chain. Even minor disruptions can have ripple effects that hugely impact subsequent steps in the production process.
Since the outbreak of the COVID-19 pandemic, many countries had to close their borders and enforce strict quarantine measures to protect themselves. This posed an issue for our ever-connected world. These restrictions severely strained supply chains and meant that many services that require on-site installation and presence could not function as normal.
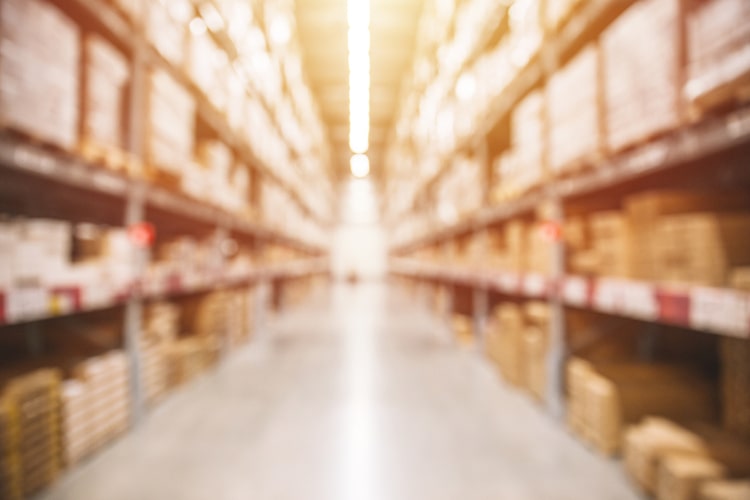
What research into manufacturing decentralization tells us
An interesting paper from 2018 looked at decentralized manufacturing (DCM) in the post-Brexit United Kingdom. The research focused on the manufacture and distribution of cell and gene therapy (CGT) products. Given the perishable nature of these products, they are sensitive to time-critical transportation, which is undesirable without proper cold chain controls in place. A decentralized network would allow smaller production facilities to be spread geographically and closer to where demand is needed. When applying the DCM model to the broader industry, one of the challenges of this system is maintaining site-to-site batch reproducibility. The rise of Industry 4.0 brings with it the dawn of the smart factory. With increased capabilities, manufacturers have remote access to real-time process data, allowing them to predict and amend issues before they arise. As this data can be accessed anywhere, it can be shared between manufacturing sites anywhere in the world. This is a pivotal factor in making accurate, efficient, and risk-averse process transfers a reality.
This paper also pointed to the socioeconomic and environmental benefits of DCM:
“DCM is an attractive proposition for personalized medicine. In this period of growing concern over efficient use of energy, avoidance of waste and the environmental impact of long-distance, temperature-controlled shipping, there is an extra driver to manufacture close to the point of use”
Using Industry 4.0 as a tool to get there
What’s interesting is this research noted the benefits of Industry 4.0 long before the onset of the global pandemic. The author identifies the practical gains from shifting away from a centralized manufacturing model to a decentralized one. Following on from the impact of COVID-19, it’s clear that industry will challenge the conventional ways of doing things and seek more robust alternatives.
Historically, manufactures have offshored production and relied on lean manufacturing methodologies to bring about efficiencies. Now the question must be asked if we were to bring back onshore manufacturing strategies and forge more robust supply chains, how would we meet and exceed efficiency targets? Industry 4.0 allows us to maintain the gains we’ve already established and significantly build on them. With previously unseen levels of process insight and hyper-connectivity, we can effectively transfer processes to multiple sites around the world and construct a more resilient supply chain. A key pillar of this new approach would be equipment capable of delivering all the capabilities needed to achieve this vision.
Multeye2 is a multipoint Near-Infrared (NIR) spectrometer designed for real-time, in-line process monitoring. It’s the ideal tool for advanced development and manufacturing and gives you the insight needed for successful product transfer, anywhere from India to Indiana. To learn how Multeye2 can kick-start your transition to the smart factory of the future, get in touch.
At InnoGlobal Technology (formerly Innopharma Technology), we’re motivated to push boundaries within industry and share our knowledge. Follow us on LinkedIn and Twitter for more exciting developments, from R&D to Industry 4.0!