ATEX Equipment Classification
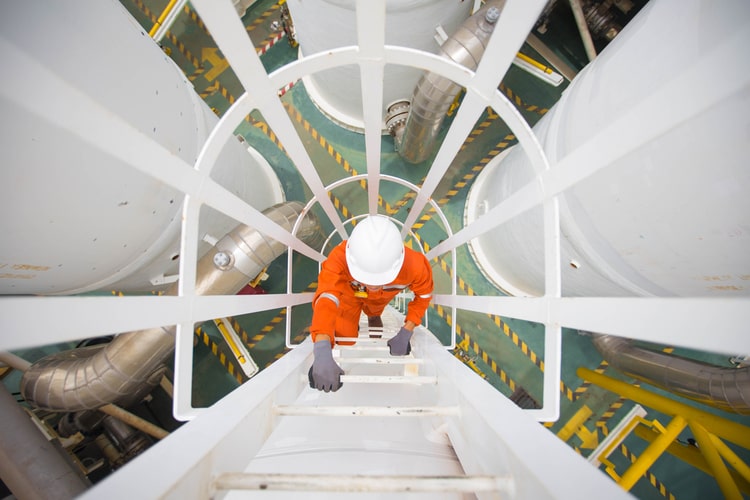
In part 1 of our ATEX blog series, we set about demystifying the often confusing world of ATEX markings. In this second blog, we will delve into ATEX equipment classification to add more clarity to the subject, while using our particle size analyser Eyecon2 as an example.
Equipment is classified as either suitable for underground mining ‘I’ operations or classified as ‘II’ for non-mining environments. This second categorisation is applicable to most other industrial applications, such as chemical, gas, and pharmaceutical, to name a few examples.
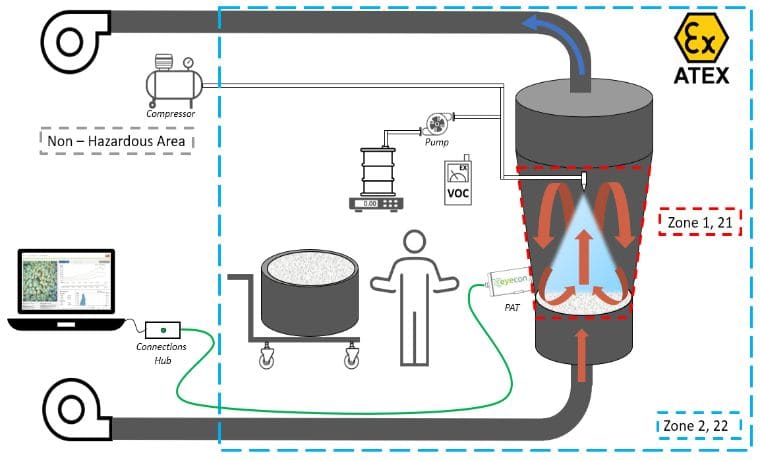
Breaking down ATEX labels
To add to the confusion, the ATEX zones we just mentioned are not directly displayed on equipment specification sheets or plates. Instead, a single number arranging from 1-3 indicates the 0-2 in the zoning nomenclature. Confused? Yes, we agree!
This classification is succeeded by a capital G or D to indicate its safety for combustible dust or gas applications. The ATEX marking, or ‘Ex’, is at the start of each line of the ATEX marking. As an example, “ II 3 GD” indicates the equipment is declared safe to use in “II” non-mining applications in Zones 2 22 “3 GD”.
Temperature classes (T1 – T6) are used to classify the maximum temperature a device is expected to generate. In order to assess the classification, the expected ambient temperature should be quantified. So for instance, if the expected ambient temperature is 0 – 40⁰C, and the Equipment operates up to 100⁰C above ambient the temperature, the device is classified as T3 (<200⁰C). The table below signifies the relationship between temperature (celsius) and temperature class.
Temperate Class | Temperature (Celsius) |
T1 | <450⁰ |
T2 | <300⁰ |
T3 | <200⁰ |
T4 | <135⁰ |
T5 | <100⁰ |
T6 | <85⁰ |
Along with the temperature rating, equipment that produces electrical or optical energy must be assessed to quantify emitted energy to allow the ignition risk to be assessed. These are assessed for both dust and gas and appear separately on specification sheets. Below, is a non-exhaustive list of some of these markings and their meanings.
Marking | Meaning |
ic | Energy Limited |
ec | Constructed to ensure no Spark or Arc risk |
op | Optical energy inherently safe |
is | Intrinsically safe. |
The gas section will include “II”, followed by a capital letter, whereas the dust section will include “III”, followed by a capital letter. In both cases, the capital letter indicates the permitted environment, be it gas or dust. Below, you will find a table of gas and dust classifications.
ATEX and Eyecon2
Eyecon2 particle sizer is a piece of Process Analytical Technology (PAT) for analysing and controlling manufacturing through real-time measurements of critical quality and performance attributes of in-process materials and processes. ATEX is a key consideration prior to installation. Eyecon2 has been designed to meet the ATEX requirements for harsh industrial applications.
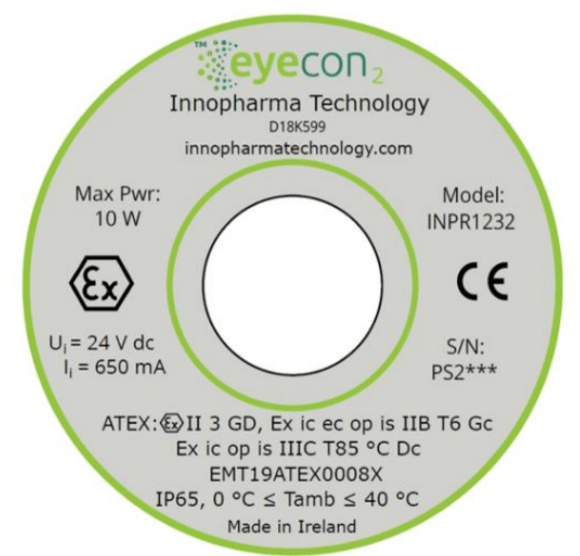
Non-contact
When considering equipment for your facility, it is important to consider placement. A misconception is that the zone inside the equipment is relevant when determining the appropriate ATEX category of the equipment. Eyecon2 is designed for placement in Zone 2, 22, observing the process through a window. The non-product contact nature allows it to observe a Zone 0 process.
Low energy
In operation, Eyecon2 is a low energy device and is intrinsically safe for Zone 2, 22 applications where volatile gases are present such as ethylene, propane and methane and also intrinsically safe for conductive dust.
IP-Rating
Eyecon2 has an Ingress Protection rating of IP65. The 6 for solids means the device is completely sealed from dust and the 5 for water means it is protected against low-pressure water from a nozzle.
Optical Intensity
The intensity of the Illumination system is limited to 15mW and is safe for all dust and gas applications.
Additional considerations
- The Eyecon2 connections hub is intrinsically safe but must be located outside the explosion hazardous areas.
- All Eyecon2 units come ATEX compliant
- Variants of the Eyecon2 are available with the IECEx (International Electrotechnical Commission Explosive). Typically, both ATEX and IECEx require compliance with the same technical standards. ATEX is driven by EU law and IECEx is a voluntary international certification scheme
If you require more information on any aspect of ATEX to further demystify the subject, get in touch!