A COVID-19 Vaccine Is Coming, but Can We Make It Safe, Fast and Effective Enough?
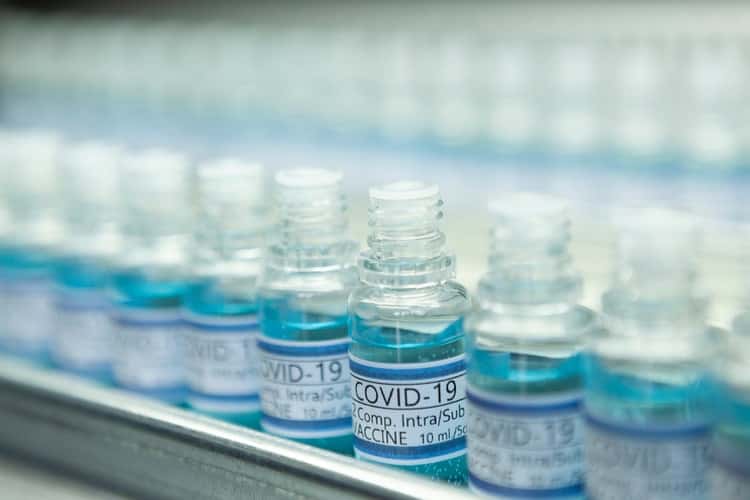
Many of the world’s leading pharmaceutical companies are locked in a race to produce a viable and safe vaccine to combat COVID-19. 2021 may be the year we see promising vaccines gain approval and enter production, but do we have the manufacturing capability to rapidly scale production to meet feverish global demand?
To date, there are over 40 vaccines in clinical trials, and at least 88 preclinical vaccines being investigated via animal testing the world over. Industry and Academia are both at the forefront of development and discovery, with the notable example of the AstraZeneca-University of Oxford partnership showing protection in monkeys earlier this summer. In reflection of these efforts, the European Union reached an agreement with AstraZeneca to deliver 400 million doses of their vaccines, provided they show positive results.
With many potential sources of a viable vaccine, and many coming from institutions without a manufacturing background, the race becomes more complicated. These institutes must finalise deals with contract manufacturing organisations (CMO) who can scale production for them. Scaling requires tech transfers, which manufacturing control systems can help with by ‘fingerprinting’ a process in one location for replication in another. Smart systems like these make scaling easier both technically and from a regulatory standpoint, ensuring a vaccine gets to market faster.
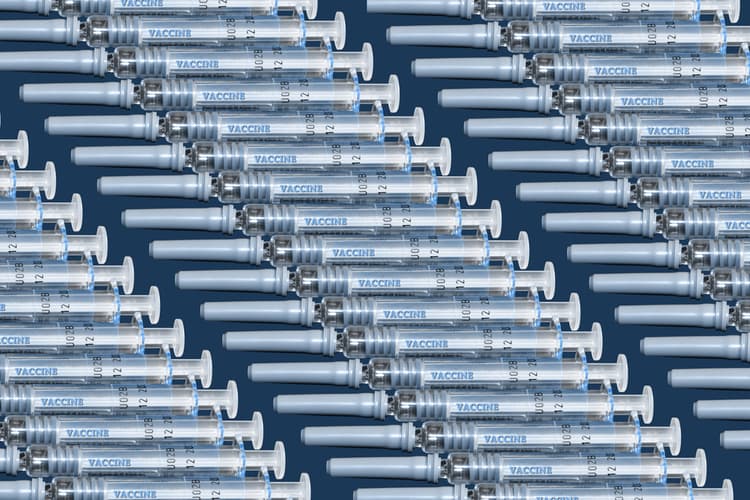
Overcoming traditional hurdles
Traditional vaccine manufacturing is lengthy and highly complex. As vaccines are biological products, they require careful consideration at all steps of the manufacturing and distribution process. Intense scrutiny is placed upon raw materials used in the initial stages of production and purification, but also when developing the antigen. Each stage in this manufacturing system relies on the highest standards of Good Manufacturing Practice (GMP), Good Laboratory Practice (GLP) and Good Distribution Practice (GDP). In total, it can take between 12-36 months to manufacture a traditional vaccine alone.
So with no time to spare and a globalised effort to roll-out an effective vaccine, how can we supercharge traditional vaccine production and bring it into the 21st century to hit these immense targets?
The factory of the future is rapidly becoming the factory of today. With a highly connected web comprising of both man and machine, considerable leaps in process insight, prediction and data management can be achieved like never before. As the pandemic restricts our movement, smart systems and smart factories ensure critical information is made available to personnel in real-time, anywhere, at any time. These advances allow for robust manufacturing processes that can operate as effectively remotely as they do with physical man-machine interaction.
One of the strongest boons of Industry 4.0-enhanced technologies is the modernisation of data management and data integrity. Typically, data generated during research and development is not handled as efficiently as production data that is more rigorously regulated, and it can be spread between multiple systems. Scattered datasets lead to highly formative data becoming a challenge to access, with the risk of critical insights getting missed as production scales to commercial manufacturing.
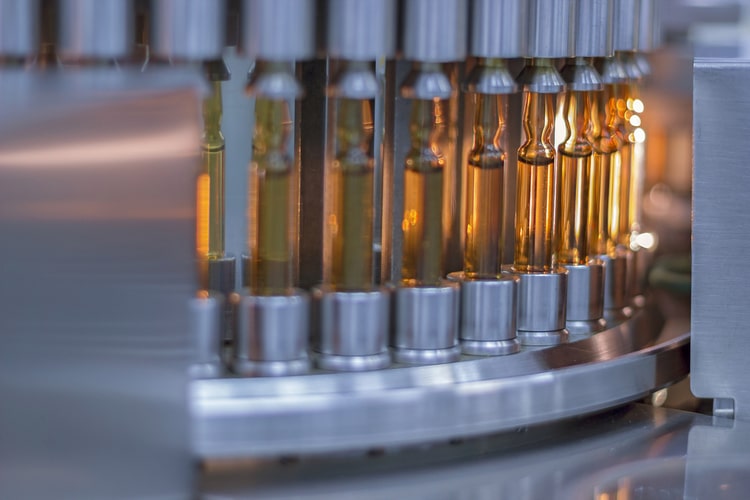
Future-proof manufacturing
Despite the long lead time of vaccine production, there is a large pool of industrial and academic players working through R&D and trialling activities. Do they run the risk of missing crucial information that would otherwise lead to a smoother, quicker, and more effective scale-up to commercial manufacturing?
With Industry 4.0 systems such as our SmartX process automation platform, manufacturers can increase process knowledge and understanding considerably. Designed with ease of integration in mind, SmartX provides opportunities for improved risk mitigation due to missed insights. As the lead time for vaccine production is primarily caused by the need for many necessary quality considerations, we must then look to inject new levels of efficiency into each step of the manufacturing and distribution journey to reduce the timeline for vaccine delivery.
Smart factories empower us to gain better process control and understanding, leading to reduced nonconformance, and wastage, while increasing yields. The hyperconnected nature of such systems allows us to access the right knowledge and data at our fingertips. In this way, SmartX bolsters lean methodology practices to permit products to get to market faster, with higher levels of quality and success.
To learn how you can build the factory of the future, get in touch!