Process Automation by the Real Experts
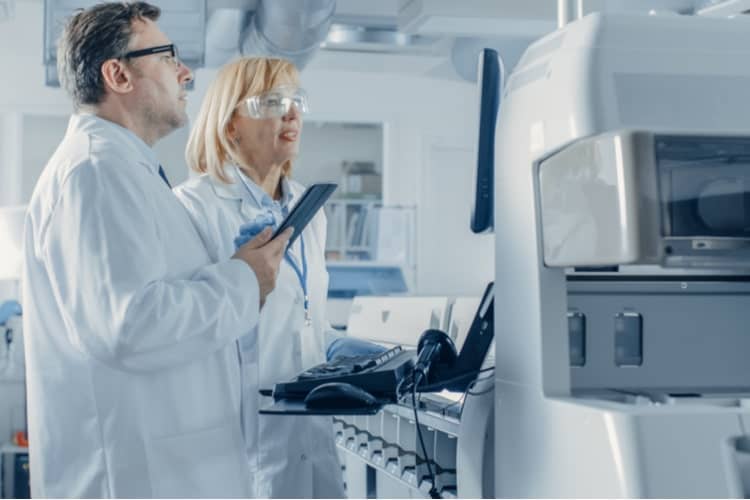
Process automation has been around for a long time, and extolling its virtues is nothing new. In Pharma, however, it has been slower to catch-on than in many other industries. This is commonly put down to the heavily regulated nature of the environment, which was certainly a valid point for some time. With regulators, particularly the FDA, moving in more recent years to fund research consortia into process control and automation, particularly in continuous manufacturing, it does seem that there is a much more defined pathway to automation now for those ready and able to take it.
This leads to the other big challenge to adoption of deeper levels of process automation in Pharma –complexity. Of course, automation is a complex proposition in any industry, but the nature of some processes in Pharma adds to this. Particularly in longer batch-processes, such as fluid bed granulation or drying, the effect of an input change can have a markedly different impact on the process depending on the point in time at which it occurs. These complex variable interrelations have inspired many a PhD thesis on modelling of fluid bed processes, but little exists still in terms of practical tools to assist in process design beyond basic physical airflow models and psychrometric moisture calculations, which at best calculate a starting point for exploring the control space.
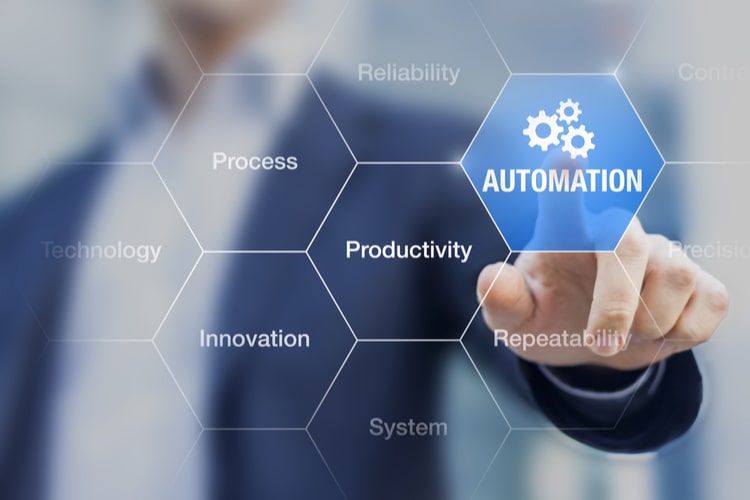
So how are these processes designed and developed today? By process experts of course! People with sharp eyes and ears, a “feel for the process”, and an extensive combination of practical experience and theoretical knowledge of the process type and equipment. These are the people best equipped to deal with the complexities of the process design and to build the logic required to automate. However, there is a further complexity challenge in the form of the automation system itself. Traditionally these systems have required a significant level of coding ability to use and/or deep familiarity with specific mathematical techniques such as model predictive control. This requires a cross-functional team to implement the vision of the process expert, resulting in a less lean and flexible process, and often diluted capability due to resource constraints.
InnoGlobal Technology’s (formerly Innopharma Technology) SmartX process automation platform takes a different approach to deliver comprehensive process automation. Automation logic is built through an easy-to-use drag & drop secure cloud interface, allowing the process expert to implement automation directly with a minimal learning curve. The logical “blocks” in this interface are developed by us to deliver flexible process-specific control methodologies, and we’re always happy to work with the experts to develop this toolset further to cope with the unique conditions and requirements of their processes.
At InnoGlobal Technology (formerly Innopharma Technology), we’re driven to push the boundaries of industry and share our knowledge. Follow us on LinkedIn and Twitter for more exciting developments in trailblazing R&D and Industry 4.0!