Making Cosmetics Safer
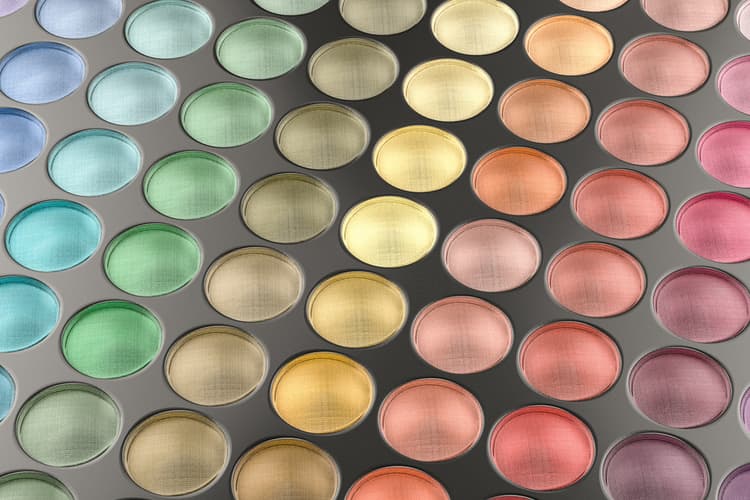
In our last blog, we explored the rise of the modern cosmetics industry and assessing the safety of making cosmetics. From the start, humans have been interested in the visual, appearance-altering aspects of cosmetics. But now, our focus is equally spent on making products safer and easier to manufacture. As technology advanced and new materials were discovered, we didn’t always have the greatest track record in product safety.
In the past, we sometimes used materials when making cosmetics without knowing their long-term effects. The use of lead powders was widespread throughout the 17th century when both men and women adorned powdery white faces laden with lead. This substance was known as Venetian Ceruse. An obvious danger to us today, but at the time, it was seen as a cultural symbol of wealth and prosperity. Queen Elizabeth I was said to have adored thick layers of the lead-based powder to hide deep smallpox scars. Venetian Ceruse was later classified as a poison 31 years after her death in 1603.
The role of the FDA in cosmetics
Modern cosmetics safety standards have progressed significantly since those days, with the FDA bearing the authority to:
- Ban or restrict ingredients due to safety concerns
- Implement product recalls
- Mandate warning labels on products
- Carry out inspections of cosmetics manufacturing facilities
- Issue warning letters
- Seize illegal products
- Prosecute violators
Many chemical ingredients are stringently assessed and prohibited by the FDA for use in cosmetics due to safety concerns. Among the list of restricted ingredients is vinyl-chloride. This ingredient was used in hair sprays but became prohibited due to carcinogenic concerns and its effect on the central nervous system. Chloroform is also on the list of banned substances following the development of liver tumors in rodents over a lifetime of oral ingestion. Even the safety of color additives must be shown to gain FDA approval, proving the vital role the regulator plays in maintaining safety within cosmetics manufacturing.
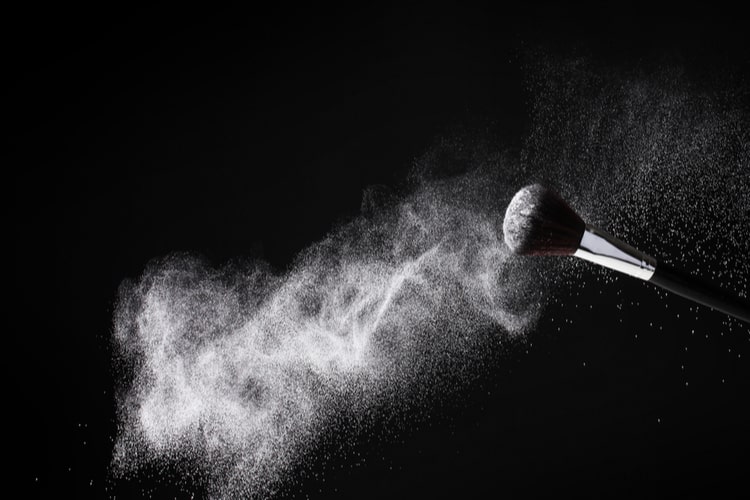
Assessing cosmetic safety
A recent study assessed the safety of boron nitride. Boron nitride is commonly used in cosmetics to help other ingredients flow more easily. It functions similarly to graphite but is prized for being chemically non-reactive. Its powdered form varies by trade name and grade, but its particle size ranges between 1 – 47 µm. Boron nitride can be found in concentrations as high as 25% for products like mascaras and eye shadows, where its smoothness-providing properties shine. The study drew attention to high boron nitride concentrations which signaled for a safety assessment. It stated:
Products containing boron nitride may be applied to the eye area (≤25% in eye product formulations), could possibly be ingested (2% in lipstick formulations), or may possibly be inhaled (≤16% in powders and at up to 0.9% in fragrance preparations)
This study noted that 95% to 99% of the particles released from cosmetic sprays have a particle size range between 10 – 110 µm, meaning they are deposited to the nasopharyngeal region (the upper part of your throat, behind the nose). Because of its particle size range, boron nitride is not respirable in any significant amount. The study then concluded that boron nitride is not expected to have chemical activity in biological systems. Although the particles in the case were deposited within the respiratory tract and presented no toxicological concerns, we can get an understanding of how important it is to maintain safe particle sizes in cosmetics. Smaller particles can penetrate more deeply into the respiratory tract with the potential for adverse effects in some cases. This leads us to consider strategies to maintain precise control of particle size using the right tools.
Eyecon2 is a direct imaging particle analyser that generates real-time particle size and shape information ranging 50 -5500 μm in a variety of critical processes used in cosmetics manufacturing. It delivers better process understanding and process control to achieve higher safety and quality targets. A unique feature of Eyecon2 is its non-product contact analysis and profiling of wet or dry powders and bulk solids. This means it’s right at home in cosmetics manufacturing to ensure the highest standards in safety and quality. Chat to us about how Eyecon2 can benefit you.
At InnoGlobal Technology (formerly Innopharma Technology) we’re motivated to push boundaries within industry and share our knowledge. Follow us on LinkedIn and Twitter for more exciting developments from R&D to Industry 4.0!